Exactly How Metal Stamping is Reinventing the Automotive and Aerospace Industries
Advanced Techniques in Metal Stamping for Accuracy Production
In the world of precision manufacturing, the evolution of metal marking techniques has actually been a critical pressure in accomplishing unrivaled levels of accuracy and performance. As sectors continually require finer resistances and detailed designs in their steel components, the mission for innovative methods in metal marking has actually heightened. From the usage of sophisticated multi-stage marking procedures to the combination of sophisticated automation modern technologies, the landscape of steel marking is undergoing an extensive transformation. In this vibrant sector, the merging of advancement and accuracy is reshaping the opportunities of what can be achieved in metal fabrication.
Advanced Multi-Stage Stamping Processes
Reviewing the intricacies of sophisticated multi-stage marking processes exposes the innovative techniques employed in modern-day production methods. Metal Stamping. Multi-stage marking is a complicated process that entails multiple actions to transform a flat sheet of metal into a last stamped item. Making use of progressive dies, where different operations are executed at each phase of the stamping procedure, permits high accuracy and performance in the production of complex metal components
Throughout the first phases of multi-stage stamping, the flat steel sheet is fed right into the marking press, where a collection of passes away are utilized to reduce and shape the product. Succeeding phases involve extra developing, flexing, and punching procedures to additional refine the component. Each stage is meticulously designed to construct upon the previous one, resulting in the development of intricate geometries with limited resistances.
Advanced multi-stage marking processes require a high degree of experience and precision to guarantee the high quality and consistency of the stamped components. By using innovative machinery and tooling, suppliers can create a wide variety of metal elements with efficiency and precision.
Precision Tooling Innovations
Accuracy tooling technologies have actually reinvented the metal marking sector, enhancing effectiveness and top quality in manufacturing procedures. These developments have significantly affected the method metal elements are generated, leading to higher accuracy and consistency in the end products. One key innovation is the advancement of computer mathematical control (CNC) modern technology in tooling design and fabrication. CNC systems allow for elaborate layouts to be equated directly into tooling, making sure precision and repeatability in the marking procedure.
Moreover, the combination of sensing units and real-time tracking abilities in accuracy tooling has made it possible for makers to find and resolve problems immediately, minimizing downtime and minimizing scrap rates. By integrating clever modern technology into tooling, drivers can optimize criteria such as pressure, speed, and alignment during the stamping operation, resulting in improved product high quality and raised efficiency.
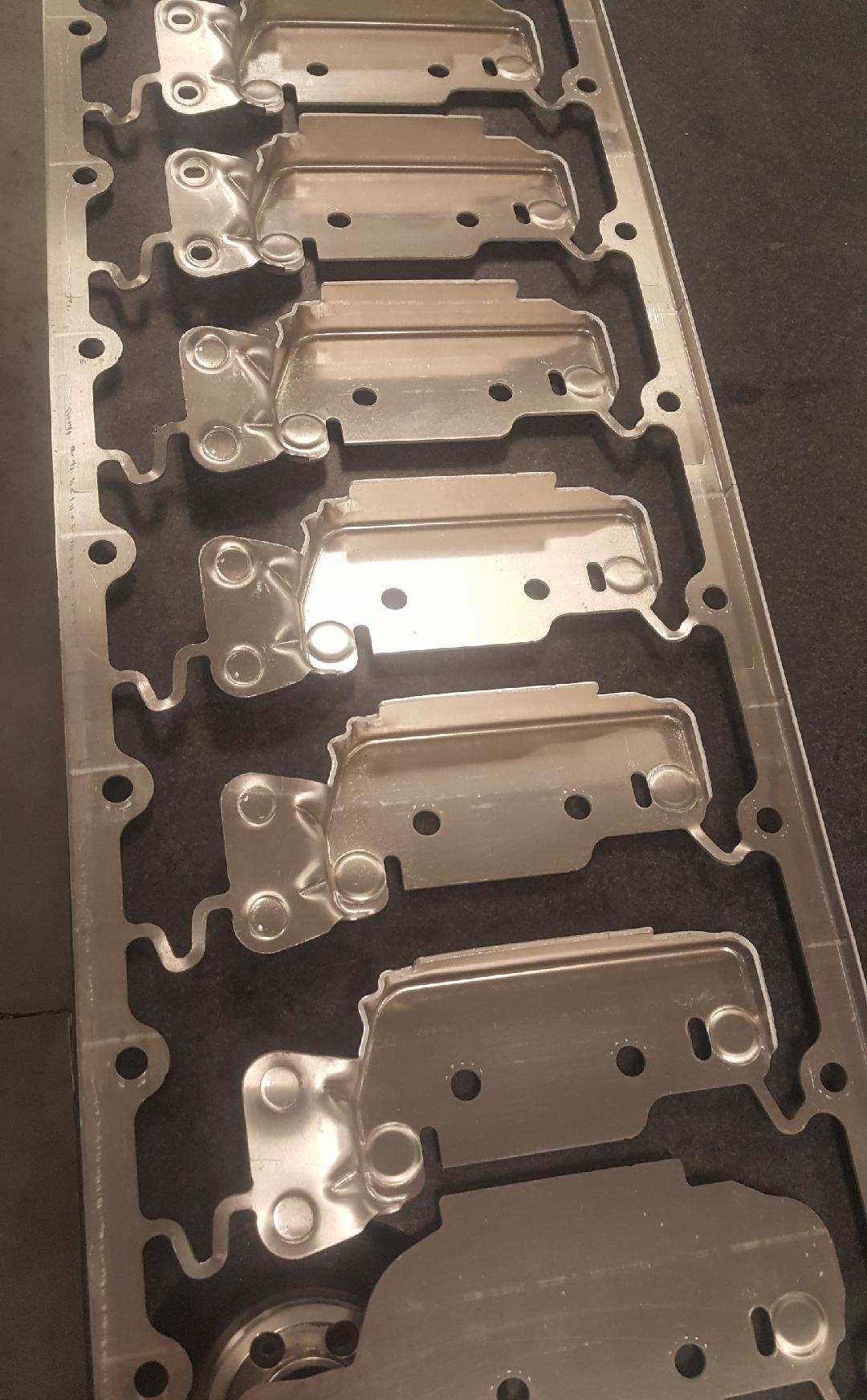
Automation in Steel Stamping
The advancement of precision tooling technologies in the metal stamping industry has paved the means for substantial improvements in automation, changing the manufacturing landscape towards raised effectiveness and performance. Metal Stamping. Automation in metal stamping involves using sophisticated equipment and robotics to do various tasks commonly executed by human operators. This shift in the direction of automation provides many benefits, consisting of enhanced accuracy, faster manufacturing cycles, and reduced labor prices
One trick aspect of automation in steel marking is the execution of computer mathematical control (CNC) systems, which allow specific control over the marking procedure. CNC innovation enables for the creation of complicated and elaborate metal get rid of constant high quality. Furthermore, automated systems can be programmed to run continually, bring about greater outcome rates and shorter preparations.
Furthermore, automation boosts workplace safety and security by decreasing hand-operated handling of moved here hefty products and decreasing the risk of mishaps (Metal Stamping). As manufacturing industries remain to welcome automation, the future of steel marking holds wonderful promise for also higher efficiency and technology
High-Speed Stamping Methods
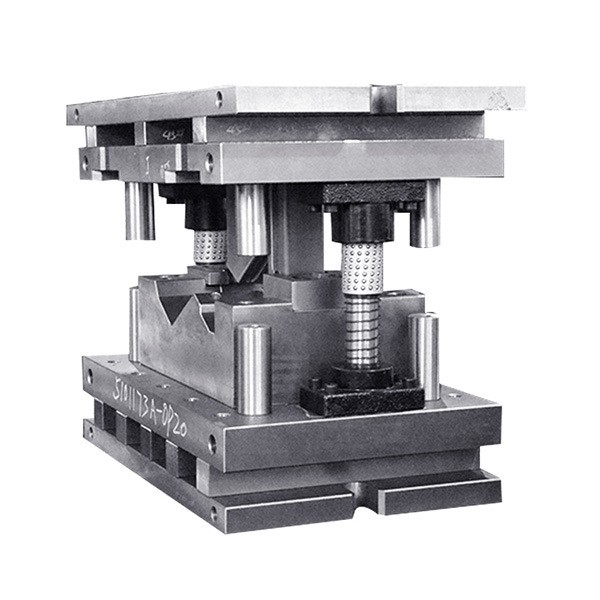
One of the key advantages of high-speed stamping techniques is the ability to create a huge volume of components in a shorter amount of time contrasted to standard stamping techniques. This increased performance not just enables manufacturers to satisfy tight production target dates however additionally makes it possible for cost savings with economic climates of scale. Furthermore, high-speed marking can help in reducing material waste by optimizing the material usage throughout the marking process.
In addition, high-speed stamping strategies typically integrate innovative functions such as fast die modification systems and real-time tracking capacities, additionally boosting the overall efficiency and versatility of the metal marking process. As modern technology remains to development, high-speed stamping is anticipated to play a vital duty in driving the future of accuracy manufacturing.
Quality Assurance in Stamping Workflow
Reliable quality assurance steps are crucial for making certain the reliability and consistency of metal stamping operations. Quality control in marking procedures entails a collection of methodical procedures targeted at detecting and protecting against defects in the manufactured components. One important aspect of quality control in steel stamping is making use of sophisticated assessment methods such as optical inspection systems and coordinate gauging devices (CMMs) to verify the measurements and resistances of stamped components.
Furthermore, quality assurance steps in stamping procedures typically consist of the application of analytical procedure control (SPC) methods to keep an eye on the production process in real-time and make certain that it stays within acceptable restrictions. By evaluating information and determining patterns, find here manufacturers can proactively attend to any kind of variances from the wanted top quality criteria.
Furthermore, quality assurance in steel marking operations likewise includes complete material testing to guarantee that the raw products used meet the called for requirements for the marking process. This may consist of conducting material hardness examinations, tensile toughness examinations, and dimensional evaluations to ensure the high quality and honesty of the stamped parts. In general, implementing durable quality assurance steps is important for attaining high-grade stamped parts consistently.
Conclusion
To conclude, progressed techniques in steel stamping play a vital role in precision production processes. Via multi-stage stamping processes, ingenious tooling solutions, automation, high-speed techniques, and rigorous quality assurance steps, suppliers can attain greater degrees of precision and performance in their procedures. These improvements in metal stamping modern technology have made it possible for firms to create intricate parts with tight tolerances, inevitably causing enhanced product quality and client contentment in the production market.